Concrete Casting Mix Products and Casting Supplies by SureCrete
XS Bag Mix
XS Colorants
Sealers and Accessories
Concrete Casting Bag Mixes
Concrete PreCast countertop and casting mixes are made easy to use with high early strength pre-blended two component mix designs.
Concrete Countertops Mix Pourable Casting Blend XS-Precast™
Blended 50 Pound Bag Terrazzo Casting Mix Complete Kit XS-Terrazzo™
GFRC Face Mix – Thin Coating Concrete Casting Spray Mix XS-Face™
GFRC Backer Mix for Reinforcement for Casting Concrete XS-Backer™
Pourable Concrete Casting Products:
Pourable cast concrete has always been an “I do it my way” kind of industry, until today. With our new pre-blended, fiber-enhanced pourable concrete bag mixes, we take the guesswork and trial and error out of your decorative cast pieces. Whether you’re interested in product concrete casting your kitchen countertop or maybe even making your wall sconces, we have a product that will make your job as easy as mold, pour, de-mold.
For those looking to cast m their pieces, we provide our XS Precast and XS Terrazzo products mix lines. XS Precast is probably the most versatile pre-blended high concrete casting mix on the market today and will easily help you create any project you can imagine. The XS Terrazzo product line is nearly identical to the XS Precast, with the very large exception of being able to load in up to 80 lbs of your choice of aggregate.
For a more traditional casting approach, we’ve designed our XS Cast-in-Place bag mix to help those looking to cast pieces the way they are used to doing it, but with the added strength and workability provided by our Xtreme Series formulas.
GFRC Concrete Concrete Products:
While Glass Fiber Reinforced Concrete is relatively new in the concrete industry, at SureCrete, we’ve managed to innovate it anyway. One of the biggest complaints we hear from casting experts is not having the same consistency of mix when going from one batch to the next – especially if the project leaders aren’t able to measure out all the ingredients themselves. We took the guess-work out of that equation and made a hybrid GFRC mix design that could be purchased already pre-blended in a 50-lb bag. Now you can get the same blend every single time you open up a bag.
and a pourable Our GFRC products are available in the same types expected in the industry – a spray-able facing mix (XS Face) and a pourable backing mix (XS Backer). Through the use of these two products, you can fill any mold cleanly while cutting down your overall weight by casting your pieces at a fraction of standard concrete casting thickness due to the added strength provided by the XS Backer mix.
If you’ve never used GFRC products before, trust us when we say that once you use ours, you’ll never go back to casting conventional concrete at full thickness ever again and great for GFRC panels.
Common Questions about GFRC Casting Concrete Products:
What makes it a hybrid Glass fiber reinforced concrete system?
Typical Glass fiber reinforced concrete formulas are made up of cement, sand, polymers, plasticizers, acrylics, and high amounts of AR glass fiber. The Xtreme Series technology uses cement, sand along with three types of fiber (PVA, Glass AR, and Nano). There are NO polymers and acrylics in its formula. Why is this a unique attribute? GFRC fabricators now have a larger temperature swing during the mixing and spraying stage of 45-85 degrees Fahrenheit, compared to typical 70-75 degrees with traditional formulas. The second component to this mix is the Precast Modifier; this product does not lose its potency even if it freezes during delivery of material, reducing waste and loss of time for the fabricator. The three fibers used are unique because they are pre-blended into the 50 lb bag mix.
When you take advantage of this technology, you quickly realize how it accelerates the learning curve of how to mix GFRC. The Glass AR, PVA, and nanofibers are already blended into the 50 lb bag, reducing errors during both mixing and application. The Xtreme Series material exceeds the performance of standard GFRC formulas with its impressive 10,500 PSI compressive strength and 1,450 PSI flexural strength. With all these features combined, GFRC fabricators achieve de-mold times between 8-12 hours after spraying.
What are the design restrictions for Glass fiber reinforced concrete?
The Xtreme Series Glass fiber reinforced concrete (GFRC) mix design is a blank white canvas with the ability to take on any color scheme, texture or shape you can imagine! The SureCrete Design team has seven reproducible texture finishes that are taught in the introductory PreCast Concrete 4-Day training course. These textures can be combined, used individually and altered with many different coloring agents for an unlimited color and texture combination. For the first time, concrete is a manufacturer fabrication material with consistent, reproducible looks, and finishes. Here are just three of the Xtreme Series finishes:
Why is Glass fiber reinforced concrete selected over other building materials?
Glass fiber reinforced concrete (GFRC) offers unparalleled versatility in applications such as interior and exterior wall panels, shower walls, concrete countertops, facades, lightweight architectural trim, balusters, fireplaces and many other precast opportunities. If you have experienced using traditional Glass fiber reinforced concrete (GFRC) formulas before, you realize that there is a learning curve in the precise measuring and spraying of the Face Mix.
Why is Glass fiber reinforced concrete (GFRC) selected over other building materials?
Glass fiber reinforced concrete (GFRC) offers unparalleled versatility in applications such as interior and exterior wall panels, shower walls, concrete countertops, facades, lightweight architectural trim, balusters, fireplaces and many other precast opportunities. If you have experienced using traditional Glass fiber reinforced concrete formulas before, you realize that there is a learning curve in the precise measuring and spraying of the Face Mix.
Lightweight Architectural Concrete Mix
When casting architectural concrete pieces, weight is a big factor. Utilize our lightweight concrete to reduce weight by 40% to 60%. Fire resistant due to vermiculite dosage.
Architectural Lightweight Concrete Mix
Xtreme Series Lightweight Plus3 is 60% lighter than concrete. It’s a high dose of vermiculite makes it an excellent fire resistant casting material.
For a long time, people have loved the look of concrete but wished they could use it for certain architectural pieces without having to add so much weight to their project. At SureCrete, we’ve developed a line of lighter-weight, pre-blended concrete bag mixes that can accomplish just that. These products will cut up to 57% of the weight of typical concrete even when applied at full thickness!
Depending on how much weight you are looking to drop, we have designed two products to best suit your project needs: XS Lightweight Plus 1 and XS Ultra Lightweight Plus 3, with Plus 3 being the “lighter” of the two mix designs.
We’ve seen these combinations used in a variety of applications: everything from custom-made exterior wall tiles and balustrades to faux-wood shutters and window dressings. Whatever your project needs may call for, we’re certain we can make sure you get the best product on the market from one of our many conveniently located distribution locations around the country.
Concrete Casting Color Additive Products
Utilizing the highest quality dry pigments, achieve depth and vibrancy of color in both the white cement Xtreme Series and the gray cement D-FRC bag mixes.
Concrete Casting Color Premium Powder Additive XS Color™
Concrete Countertop Veining Powder XS-Veining™
Premium Food Safe Concrete Sealers
Food safe and able to resist heat up to 300 degrees, these coatings will protect countertops, wall panels, floor tiles, and much other concrete and natural stone.
Concrete Countertop Sealer Food Safe Semi-Gloss and Matte Finishes XS-327™
Thin High Gloss Concrete Casting Sealer Xtreme Series XS PC12™
What is important when selecting a concrete casting or counter top sealer?
Using either our water-based XS-327 sealer or our XS-PC12 used to apply to protect the surface of concrete countertop sealer, you’ll be able to give your project a nice, clean coating that you can be certain will last for a very long time and protect it from all manner of chemicals, weather conditions and UV exposure.
You can have faith that your cast concrete project will last because at SureCrete we pride ourselves on staying at the forefront of protective coatings technology. We want our concrete sealers to last even longer than your concrete does!
Concrete Casting Forming and Edge Profile Products
Products to help you easily form and design your concrete cast with decorative accent edges.
Concrete Casting Forming System Foam Rails and Tapes
Concrete Countertop Edge Profiles 50 Feet 4 Designs
How do you Cast an Integral Sink in a Concrete Counter top?
Sink molds are used to create shapes on a concrete surface that become integral sinks within the surface. The sizes, shapes, and variations of each can offer a tremendous library of useful choices and looks for your client. These molds are made to use as A molds only, and the use of GFRC, Hybrid, or in-house made B forms are necessary to form these sinks. The sink molds are made of high strength tooling gel coat that with proper care will offer a lifetime of uses. The walls are five layers of marine grade glass fibers and an integral flange of fiberglass reinforcement is used to keep straight sides, prevent cupping, and give an internal flange to allow it to be pulled from the mold. Blowing the molds out with air may blow out the bottom of the sinks it is a better option to use ice to shrink the mold and pull the sink out with clamps on the internal flanges. By using these materials and entering a market of exacting standards, it is important to understand how to use the tools available through SureCrete to adhere and excel to these standards.
Sinks & Niches Steps: Countertop mold: After choosing the sink mold you want to use, you have to fasten it to the surface in some way. Most times just using silicone to adhere the sink edge to the mold surface is sufficient. A plywood insert supplied by the concrete fabricator allows for screws to be used to pull the sink mold placing down to the mold face; however, silicone is always needed to seal the seam and round the edge. The plywood block may be adhered to the inside of the sink mold return flange with hot glue, so the plywood stays positioned as the screw is fastened into the plywood.
Removal: Using an angle supported by a block of wood you can use c-clamps to put firm pressure on the sink mold. If steady pressure after sitting for 10-15 minutes does not release the mold, you can fill the sink with water and ice cooling the mold until it releases from the concrete. Make sure the block of wood is not on or directly above the sink mold, and the angle is at least 1/8” thick. In the case of A &B molds such as the round vessel mold you can use wood shims on the perimeters to put pressure on the mold parts to separate them from each other. You can also use ice to shrink the molds. Blowing air into the drain flange is a suitable method of separation of vessels only, but be careful to not build up too much pressure if your sink was not properly prepped you may crack the sink.
Care and Use: For a Lifetime of use, clean the mold after each use with a diluted 3 to 1 SCR solution. Make sure to remove build up first with a block of hard wood, while blowing clean and not letting the sand residues scratch the gel coat. When cleaning and wiping use clean sponges and towels so that residual sand will not scratch the surface. Make sure to wax after and before using the sink with Zymol blue car wax and do not refrigerate as directed. Three to four applications will give a slick film suitable to release the sink mold. Scratched sinks can be wet sanded, and the gel coat polished with a regular marine or automotive compound.
It takes a smart person to admit that sometimes you need help to get a job done right. The same principle holds true with concrete casting. You need more than just a wonderfully crafted pre-blended bag of concrete mix (like any of our Xtreme Series lines). No matter which part of the job you need a little help with; we’ve got the accessories to help make your life easier.
For help with the prep-work, we provide easy to use forms, pour molds and concrete edge form profiles so that you can lay out your designs with ease. We also supply some of the strongest and lightest fibers and rods to make sure that your placing cast mix is the strongest it can be. If you want to get creative with your XS casting products, take a look at our XS Veining, Slurry and Packing Additives as well and pigment colors before sealer.
Wherever you are located, we have a conveniently located distribution center close by for you to pick up any casting accessories you might need to make sure your precast concrete project is a success.
Concrete Casting Accessories
Concrete Casting Accessories and supplies in aiding in design look and reinforcement
Concrete Slurry Mix Pin Hole Filler for Casting XS-Slurry™
Packing Additive to Achieve Pressed Look XS-Packing Additive™
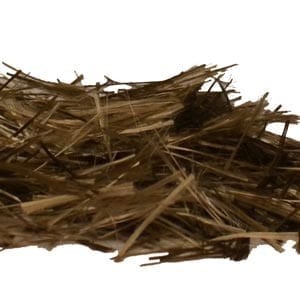
Concrete Casting Mix Products for Casting Concrete Projects
Casting mixes and sealers for creating production precast, countertops, furniture, tile and concrete wall panels project.
GFRC – Glass Fiber Reinforced Concrete:
The industries most used a pre-blended glass fiber reinforced concrete system, the use of a sprayable face coat with a fiber-rich backing coat produces unparalleled strength.
Concrete Casting Mix Pourable:
Concrete countertop and casting mixes are made easy to use with high early strength pre-blended two-component mix designs.
Lightweight Architectural Concrete Mix:
When casting architectural concrete pieces, weight is a big factor. Utilize our lightweight concrete to reduce weight by 40% to 60%. Fire resistant due to vermiculite dosage.
Pourable cast concrete has always been an “I do it my way” kind of industry, until today. With our new pre-blended, fiber-enhanced pourable concrete bag mixes, we take the guesswork and trial and error out of your decorative cast pieces. Whether you’re interested in product concrete casting your kitchen countertop or maybe even making your wall sconces, we have a product that will make your job as easy as mold, pour, de-mold.
For those looking to cast m their pieces, we provide our XS Precast and XS Terrazzo products mix lines. XS Precast is probably the most versatile pre-blended high concrete casting mix on the market today and will easily help you create any project you can imagine. The XS Terrazzo product line is nearly identical to the XS Precast, with the very large exception of being able to load in up to 80 lbs of your choice of aggregate.
For a more traditional casting approach, we’ve designed our XS Cast-in-Place bag mix to help those looking to cast pieces the way they are used to doing it, but with the added strength and workability provided by our Xtreme Series formulas.